- Home
- BLOG: NOT FOUND
- Evolution and types of extraction systems
Evolution and types of extraction systems
In the previous articles we focused on the main dosing systems and related differences in use and operation, on microdosing, on the types of conveying (both in the dilute phase and in the dense phase), on the dedusting systems and, finally, on the mechanical conveying systems.
In this article, however, we carefully delve into the functioning of the extraction systems which, over the years, with the increase in the types of raw materials and semi-finished products, have increasingly diversified.
Types of extraction systems
Vibrating extractor: allows the extraction from silos, hoppers and tanks of products that do not flow freely towards the discharge. The particular construction shapes of the bottom and of the internal diaphragm allow the vibrations to be transmitted to the silage product which ensure a continuous and regular discharge flow, eliminating the danger of the formation of "bridges" or uncontrolled flows. Furthermore, the possibility of adjusting vibrations and height make it one of the most used machines for this use.
Purely as an indication, the sizing of the vibration extractor is determined by the diameter of the upper tank (normally the diameter of the extractor is half the diameter of the tank), but it can also depend on the flow rates required in extraction which can determine the increase or the decrease in diameter.
Flat bottom extractors: this type of extractor, on the other hand, allows the extraction of products with a low degree of smoothness and difficult to extract. Its construction allows a high unloading speed and, given the reduced dimensions, it is ideal for installations in limited spaces. In addition, it is suitable for the installation of multiple simultaneous drains without limiting the storage of the upper storage tank.
Also with this machine the sizing takes place in relation to the diameter of the upper tank and allows the installation of more scraping blades inside to make the evacuation of the product constant.
In case of need to dosing the product in the unloading, it is possible to install a double flat bottom to control the extraction by adjusting the flap of the second stage of work.
Other more particular and ad hoc applications for the various uses can be made with screw bottoms: these are particular bottoms composed of two or more bridge breaker reels and an extraction auger to allow the product to flow out. This application is particularly used on products such as fibers or powders that can form blocks or lumps of product: the upper reels move or break the product, the lower auger, on the other hand, extracts or doses the product.
In addition to the machines described, it is possible to realize other extraction systems suitable for the most sticky and packing products. For example, it is possible to install cloths inside scale tanks to eliminate the friction between the powders and the metal and, by moving the cloths themselves with compressed air, the tank is emptied quickly, significantly reducing the dust that collects shape and stay inside. This application is typical in scales and tanks where products such as carbon black or dioxides are stored.
In all cases, in addition to the basic rules for sizing the machines, the definition of the machine is made through knowledge of the product to be treated, its physical and chemical characteristics, the flow rate and the spaces available.
Its extraction system for every need
As you will have understood, therefore, CAMImpianti extraction systems are made ad hoc for various needs. We are able to respond to all needs to make the most suitable extraction system for your production more efficient. To understand which system is best suited to your production cycle, we always recommend relying on the skill of professionals.
Relying on our decades of experience we will be able to advise you on the best solution. Contact us at any time.
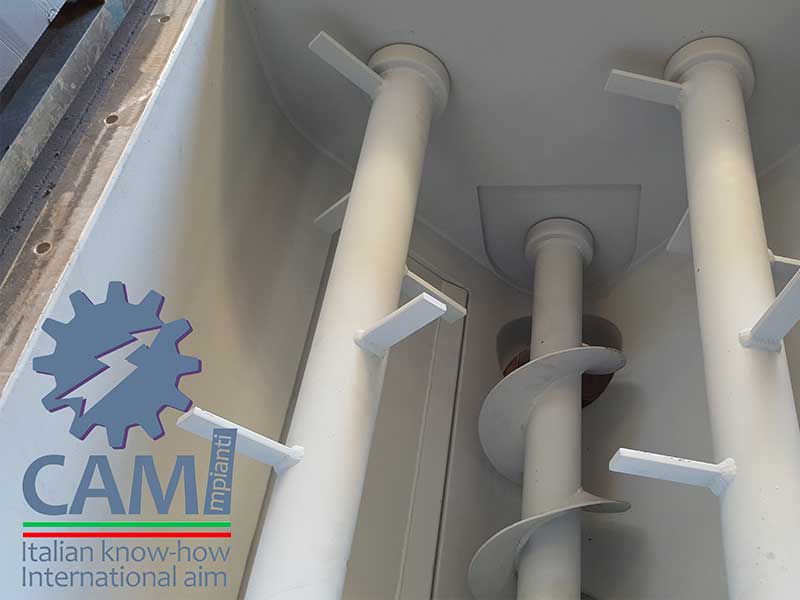
Blog
Rotary valves: functioning and types
In the previous articles we have focused on the types of transport describing their operation both in the dilute phase and in...
Importance of conveying machines in industrial processes
Pneumatic Conveying systems The quality of the machines used for conveying of the raw materials, semi-finished products and ...
Microdosing systems
Industrial machines for dosage When we are talking about dosing related to industrial machines, it is very important to know...
Mass feeder dosing systems
Industrial Machines for dosing system The Industrial Machines’ business is become more and more perfect during the tim...